Case Study: Organizing the Production of Children's Subscription Kits
The RUKI team helps companies find factories in China and manufacture products of any complexity, including subscription kits. One such project was implemented with Oyster Kit, a company that develops sets allowing children to explore various professions in a playful manner, from archaeologist to designer. Here’s how the project turned into an exciting quest involving testing game mechanics via video calls and «detective» challenges.
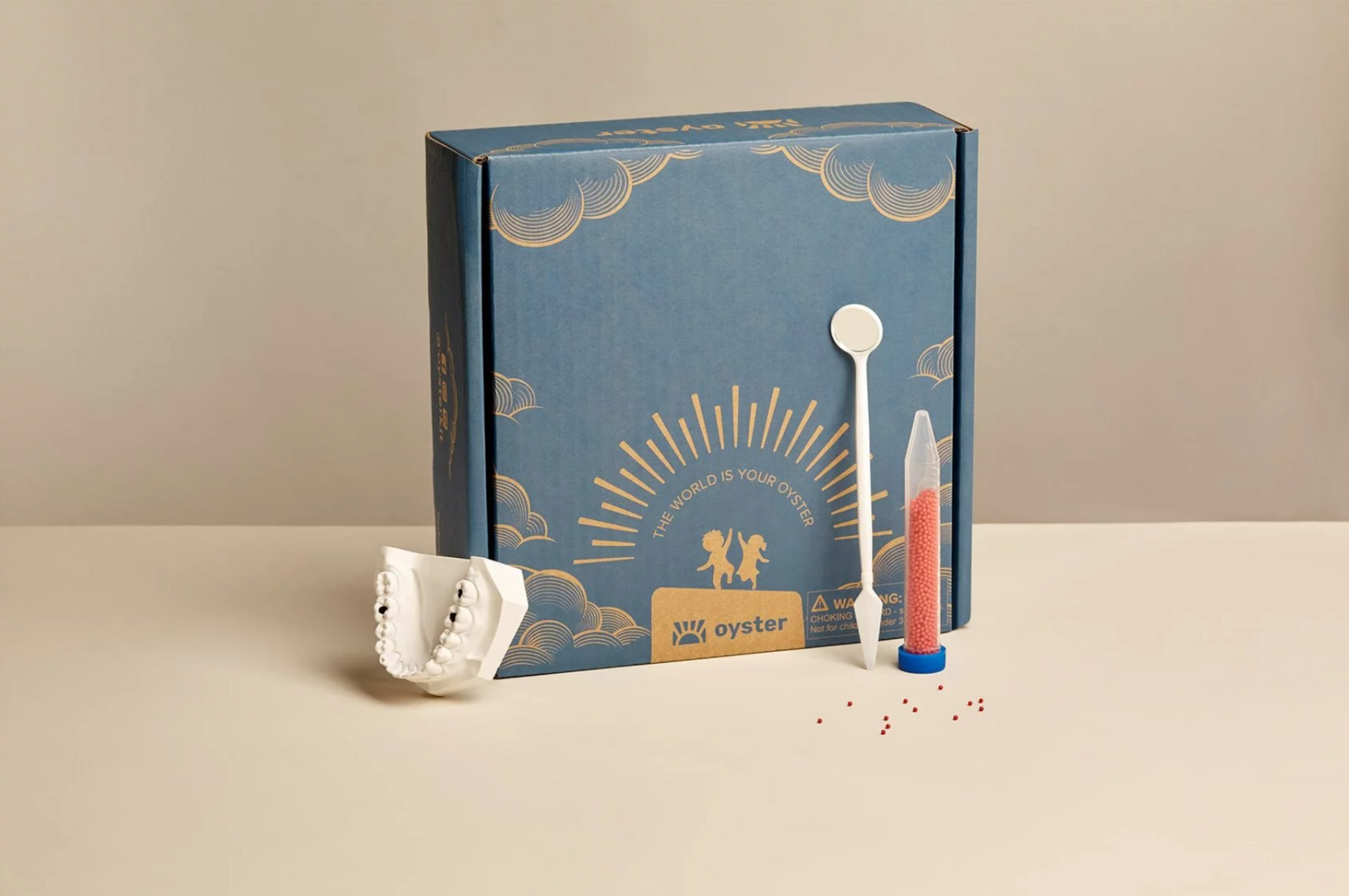
Coffee, books, food, houseplants, and even meteorite fragments — subscription boxes are growing in variety each year, and startups continue to innovate new formats. There are kits for left-handers, pug owners, instant noodle enthusiasts, and luxury watch collectors. A couple of years ago, a Bloomberg journalist conducted an experiment where she only ordered goods from box services and did not shop in stores for several weeks. The subscription box market had been growing annually by 100%, with the peak growth occurring during the COVID-19 pandemic.
Subscription box businesses have many advantages and may seem simple at first glance. However, the production and logistics of subscription boxes are complex yet interesting processes, as experienced by the RUKI team through their collaboration with Oyster Kit. The company produces educational kits for children to learn about various professions, such as engineer, archaeologist, veterinarian, artist, and detective.
Each kit requires unique game mechanics to be developed from scratch, and every component is hand-picked. For example, a toy dog in a veterinary kit needs fur of a specific smoothness, and a dentist kit needs a realistic jaw mold, complete with cavities. Furthermore, the toy dog must be ordered from one Chinese supplier, the mold from another, and the box and printing from a third. In total, hundreds of different components must be sourced for dozens of kits.
Subscription box businesses have many advantages and may seem simple at first glance. However, the production and logistics of subscription boxes are complex yet interesting processes, as experienced by the RUKI team through their collaboration with Oyster Kit. The company produces educational kits for children to learn about various professions, such as engineer, archaeologist, veterinarian, artist, and detective.
Each kit requires unique game mechanics to be developed from scratch, and every component is hand-picked. For example, a toy dog in a veterinary kit needs fur of a specific smoothness, and a dentist kit needs a realistic jaw mold, complete with cavities. Furthermore, the toy dog must be ordered from one Chinese supplier, the mold from another, and the box and printing from a third. In total, hundreds of different components must be sourced for dozens of kits.
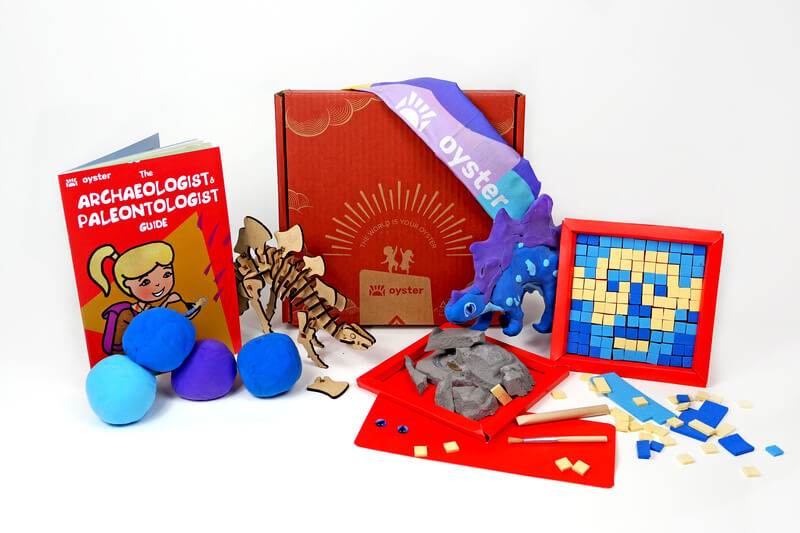
RUKI helped Oyster Kit launch the production of over 20 kits, each containing about 10-20 different components. Some parts are bought in stock and branded, while others are custom-made according to specific requirements. Every item is individually tested to ensure the appropriate density or texture is achieved. Experiments, following Oyster Kit’s instructions, are conducted to test each kit, such as assembling a catapult or performing a chemical reaction live, with the client observing to ensure everything works correctly.
Only after thorough testing are the completed kits handed over to the shipping company and sent from China to the USA (Oyster Kit’s primary market). The production process is a real quest, which can be divided into five levels.
Level 1: The Beginning - Finding the Perfect Supplier
When selecting components, several parameters must be considered, including price, quality, size, material texture, color, minimum order quantity, and composition meeting safety standards. All elements must work together, or the child won’t be able to perform the experiments described in the kit.
Finding the required component is a long and meticulous process, especially remotely. Each sample needs to be photographed and sent to the client for approval. Daily dialogues with the client look something like this:
— «Here’s the information on the toy dogs: we have a small husky and a compact schnauzer. Which one do we choose?
— The dog looks good, visually appealing. Is it smooth enough?»
Finding the required component is a long and meticulous process, especially remotely. Each sample needs to be photographed and sent to the client for approval. Daily dialogues with the client look something like this:
— «Here’s the information on the toy dogs: we have a small husky and a compact schnauzer. Which one do we choose?
— The dog looks good, visually appealing. Is it smooth enough?»
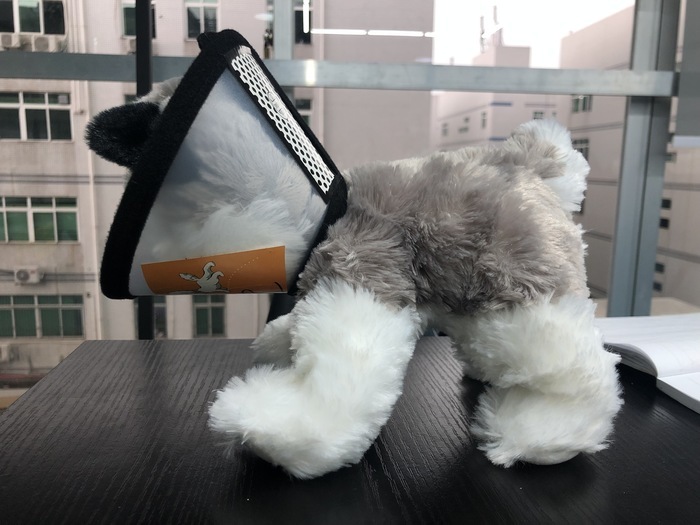
Even if the perfect supplier is found, each component is checked and tested multiple times in each new batch to eliminate errors. RUKI’s extensive database of verified factories, which they’ve worked with on products ranging from respiratory trainers to smart collars, is invaluable in this process.
On average, RUKI selects 10-15 suppliers per Oyster Kit set, with a record of 27 factories for a fashion designer kit.
All processes (including assembly and logistics) go through RUKI’s office in Shenzhen, which is equipped with its own warehouse and occupies 150 square meters. Typically, about 5 managers negotiate with factories, and 3-8 assemblers work on projects, depending on workload.
On average, RUKI selects 10-15 suppliers per Oyster Kit set, with a record of 27 factories for a fashion designer kit.
All processes (including assembly and logistics) go through RUKI’s office in Shenzhen, which is equipped with its own warehouse and occupies 150 square meters. Typically, about 5 managers negotiate with factories, and 3-8 assemblers work on projects, depending on workload.
Level 2: Accurately Calculating Timing
Agile, SCRUM, Kanban, and other methodologies can be used to manage the production process, yet something often goes awry. Experimental time management is necessary. Any item ordered not in stock requires more time to produce, even simple printing like a cardboard figure. To meet deadlines, work on several Oyster Kit sets is conducted simultaneously, with daily updates on each part posted in Basecamp.
Planning shipments requires considering both production and logistics. Delays at customs can disrupt deadlines, so contingency time for force majeure is always factored in. Certification nuances often affect material choices — Oyster Kit tries to use less plastic, but wooden components are harder to clear customs. Hence, EVA (ethylene-vinyl acetate) polymer composite components are often used. They are more eco-friendly than plastic and lighter, which is crucial. Every detail is weighed — sometimes even 10 grams of excess weight can be decisive in unit economics calculations.
Planning shipments requires considering both production and logistics. Delays at customs can disrupt deadlines, so contingency time for force majeure is always factored in. Certification nuances often affect material choices — Oyster Kit tries to use less plastic, but wooden components are harder to clear customs. Hence, EVA (ethylene-vinyl acetate) polymer composite components are often used. They are more eco-friendly than plastic and lighter, which is crucial. Every detail is weighed — sometimes even 10 grams of excess weight can be decisive in unit economics calculations.
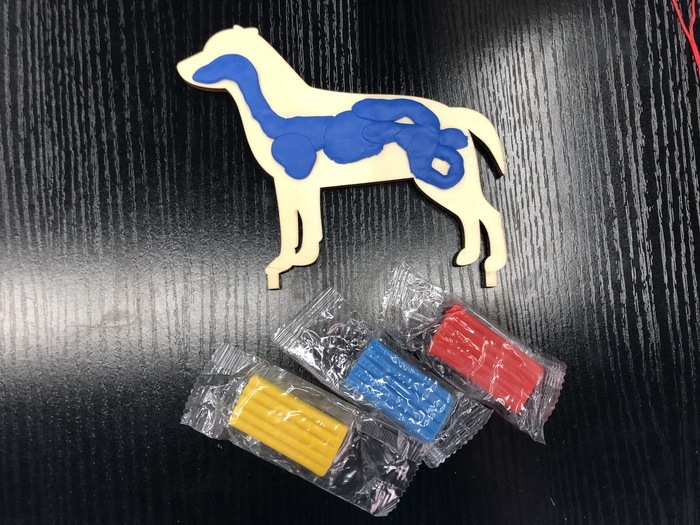
Planning shipments requires considering both production and logistics. Delays at customs can disrupt deadlines, so contingency time for force majeure is always factored in. Certification nuances often affect material choices — Oyster Kit tries to use less plastic, but wooden components are harder to clear customs. Hence, EVA (ethylene-vinyl acetate) polymer composite components are often used. They are more eco-friendly than plastic and lighter, which is crucial. Every detail is weighed — sometimes even 10 grams of excess weight can be decisive in unit economics calculations.
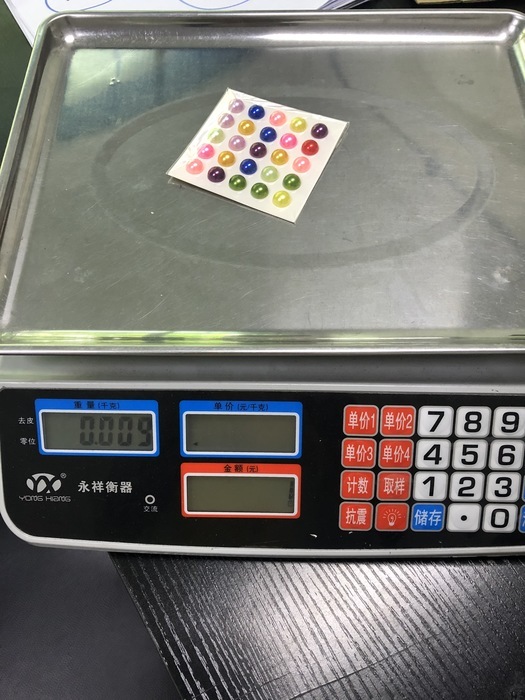
Level 3: Finding Common Ground
RUKI has been working in China for over ten years, understanding local contractors' logic and motivation. This knowledge helps prevent problems. Unrealistic deadlines and unattainable tasks are not set. In China, anything is said to be possible, but there are exceptions. For example, if a factory promises to complete an order in 14 days, three weeks are allowed for the task to ensure deadlines are met. All agreements are documented in writing and checked several times during production. An error in supplying one component jeopardizes the timely assembly and shipment of the entire batch.
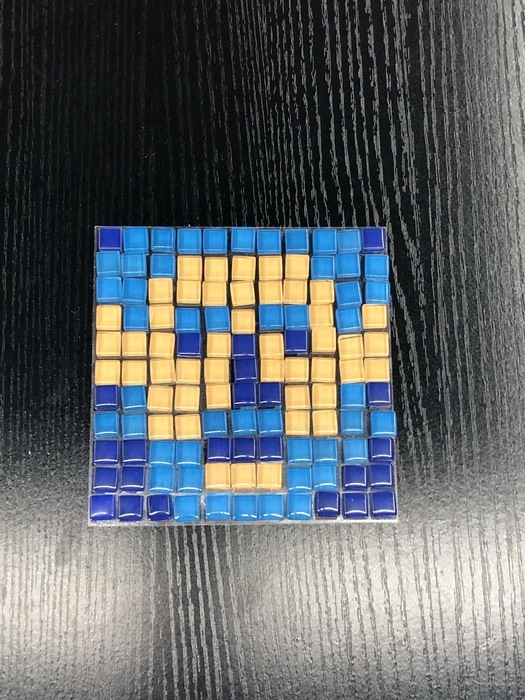
Sometimes, defects are found during quality control. Most structural defects can be detected during preliminary testing — videos are recorded, and results are confirmed with the client. If a defect is found in a batch of finished products, the manufacturer must correct the mistake at their expense, delaying delivery. This is another reason for including additional days in the production schedule.
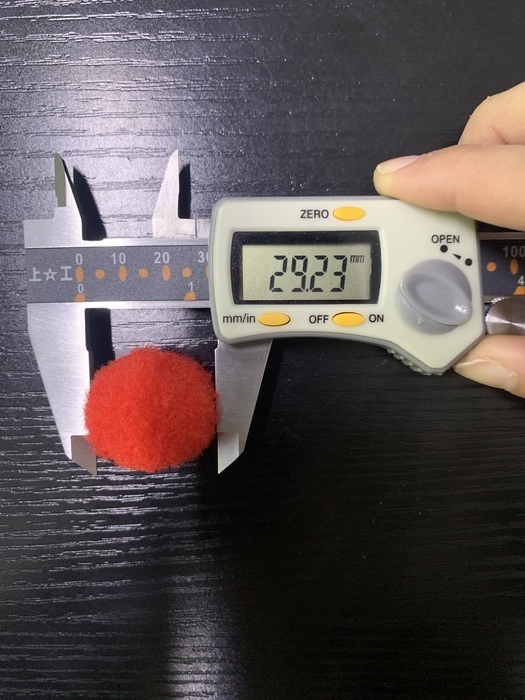
Successful project implementation, involving more than 20 people from RUKI and Oyster Kit, relies on communication. Everyone must be on the same page. Mistakes happen and must be acknowledged. Once, due to a misunderstanding, identical glasses were included in a detective kit instead of different variants. The issue was resolved by assembling the missing glasses and sending the correct sets to customers, absorbing the costs.
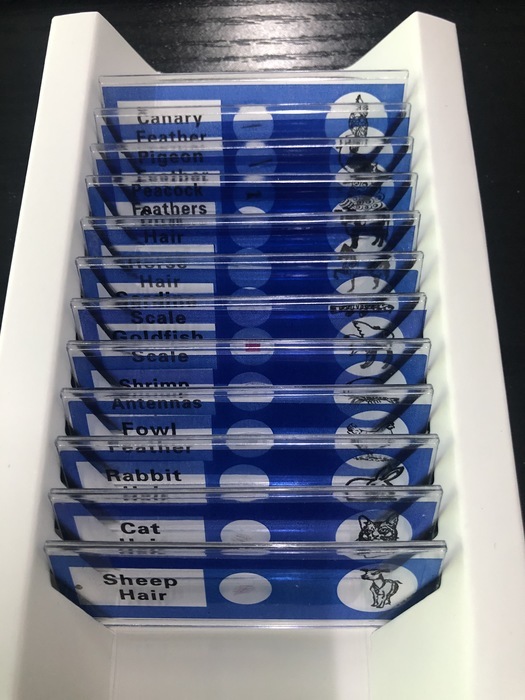
Level 4: Meeting the «Final Boss»
The most crucial stage before producing component batches is certification. For children's products, standards are stringent: experts evaluate both parameters (sharpness, size, or thinness of details) and component composition (e.g., phthalates or lead presence). Components are sent to a laboratory, and initial choices aim to avoid issues with U.S. regulatory bodies.
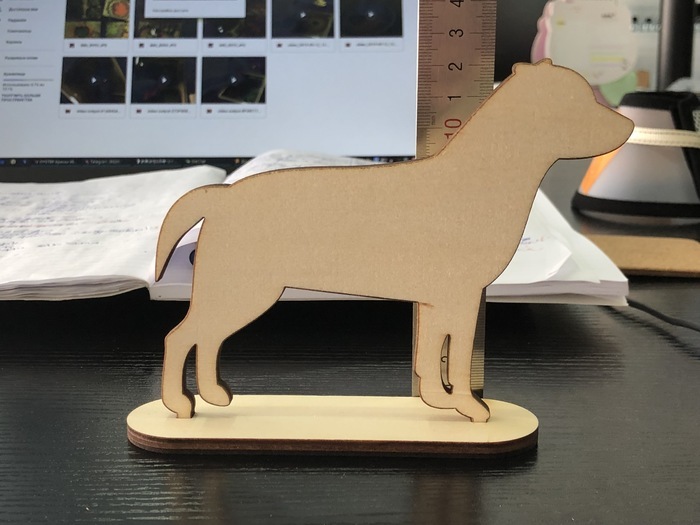
Strict certification rules sometimes prevent sets from being released. For instance, an Electrical Engineer set was too complex, with many small and sharp parts (primarily wires). The prototype included about 40 components, excluding printing, making it the most challenging set to produce. RUKI hopes to release it in the future.
Level 5: To be continued
In subscription services, the production process never ends: the line of sets expands, with new designs, components, and product categories, and old ones require changes or additions. Initially, RUKI assembled only three sets, then ten, and now regularly prototypes and produces nearly 30 sets.
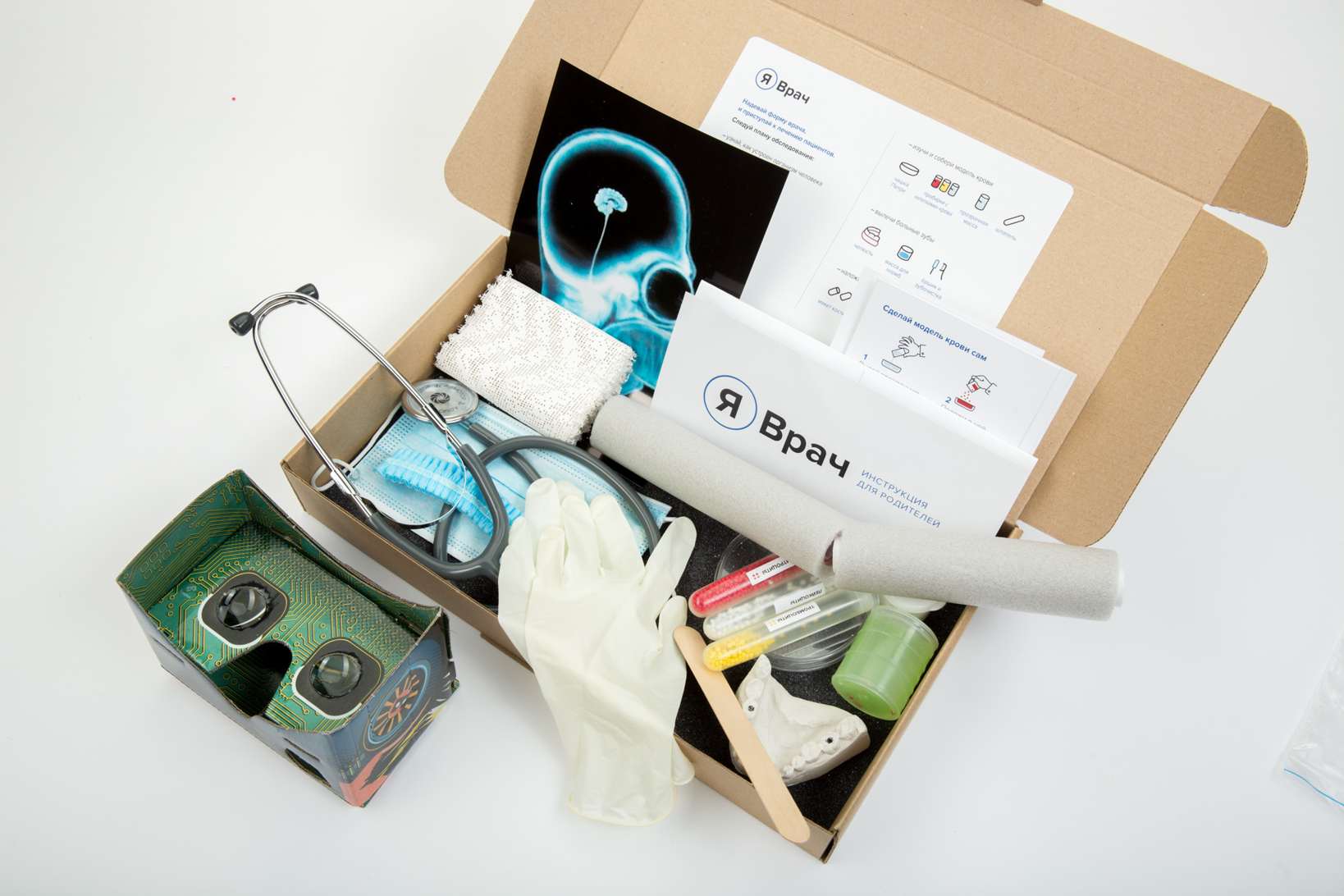
As the process progresses, RUKI gradually improves the workflow. It’s like a video game: each time the result gets better, but there’s always a desire to beat the previous record or reach a new level.